夹钢制作工艺初探
字号:T|T
2024-05-21 18:43 来源:自然科学史研究
摘要:本文梳理了与夹钢工艺有关的文献史料和考古成果,总结了中国古代夹钢制品的金相特点并对焊药进行了探讨,认为夹钢起源于汉魏时期,锻焊所用的焊药为黄泥或陈久壁土。通过对阿昌族“户撒刀”的工艺调查及样品分析,本文又侧重研究了夹钢界面、焊药及夹钢刀的性能。研究表明:夹钢户撒刀淬火后的两侧组织为铁素体和珠光体,心部夹钢层的组织为回火马氏体,界面达到了冶金结合,自回火过程减小了淬火后界面的开裂倾向。夹杂物的能谱分析表明含有SiO2的砂土焊药,在高温下与锻接表面的氧化铁形成低熔点的液态硅酸盐,起到了造渣作用。显微硬度测试结果为心部平均硬度800HV,两侧平均硬度为350HV,表明夹钢户撒刀达到了刚柔相济的性能。
夹钢是将熟铁或低碳钢作为刃器本体,在本体心部夹入中碳钢或高碳钢作为刃体的一种传统工艺,在古代被广泛用以制作工具和刃具[1-3],如图1所示。夹钢刀的优点是韧性好且刃口锋利,使用时不崩不卷。夹钢工艺在我国具有悠久的历史,然而古文献中的描述较为隐晦,考古出土的夹钢遗物也较少,造成对其起源及特点认识不足。目前研究主要集中在出土夹钢制品的金相分析和传统工艺调查。陈建立[4]、王可和韩汝玢[5]、黄秀纯[6]等对夹钢铁器进行了金相分析,从实物的角度印证了古文献有关夹钢的记载。一些学者也深入少数民族地区对夹钢传统工艺进行田野调查。较早开展研究的是汪宁生对阿昌族铁器制作的调研,不仅从自然条件、信仰和民族影响等方面分析了户撒乡阿昌族的铁器,而且还详细记录了曼东寨老铁匠采用“熟铁夹钢”制短刀的工艺过程[7],由于当时条件限制,未能搜集到产品标本。李晓岑也曾对户撒乡阿昌族的传统夹钢工艺进行过调查,并分析了阿昌族铁器的地域性特点,当地优良的水质是能打出好铁的一个重要因素[8]。以上学者详实地记述了夹钢的工序步骤,对理解夹钢起到了很大作用,但在技术细节上仍需进一步研究,如夹钢性能、界面结合难点及焊药的作用等,需对夹钢样品做微观组织及性能分析,才能有更清晰的认识。基于上述问题,本文总结了中国古代夹钢的文献记载及考古成果,结合对户撒刀的传统工艺调查和样品的材料检测分析,探讨古人对夹钢的认知和工艺难点,揭示夹钢刀的组织及性能特点。
首六寸,谓今刚关头斧。贾公彦疏:“云谓今刚关头斧者,汉时斧近刃,皆以刚铁为之,又以柄关孔,即今亦然。”[9]
“头斧”为加工木材的工具[10]。何堂坤认为此“刚铁”即刚强之铁,即钢[11]。依贾疏,汉代的斧刃为钢,暗指采用了复合材料工艺。东汉时期,炒钢的普及使得铁器最终取代了青铜器,故此斧身应为材质较软的熟铁。郑玄为东汉人,贾公彦为唐人,表明东汉和唐代的铁匠善于采用钢材质作为生产工具的刃部,虽未阐明钢的制备及使用何种方法将钢复合至刃部,却是有关夹钢最为隐晦的记载。
《北齐书》记录了南北朝时期的著名冶金家綦母怀文造宿铁刀的过程:
烧生铁精,以重柔铤,数宿则成钢。以柔铁为刀脊,浴以五牲之溺,淬以五牲之脂。[12]
“柔铤”,即可锻原料,为熟铁。“宿”原意为“隔夜”,此处为灌炼,故“数宿”应指灌炼数次。杨宽在《中国古代冶铁技术的发明和发展》中指出,“宿”为生铁和熟铁如同雄雌两性的动物宿在一起交配[13],这种解释和《天工开物》描述的灌钢较为一致:“生铁先化,渗淋熟铁之中,两情投合。”[14]“生铁精”,按照《天工开物》的记录和杨宽的解释,喻为生铁的精华。“烧生铁精,以重柔铤,数宿则成钢”为刃部的原料制备过程,即灌钢的制备。笔者认为“以柔铁为刀脊”表面上是说以柔铁作为刀脊,暗指以灌钢为刀刃,而只有夹钢工艺才能将两者复合在一起。“浴以五牲之溺,淬以五牲之脂”是采用不同的冷却介质对刀淬火的工艺。这条文献虽未直接揭示工艺细节,却是能从已知文献中推断为夹钢刀的最早文献记载,刀刃的钢料来源于灌钢,而灌钢出现在南北朝时期,结合“汉时斧近刃”,夹钢技术最晚在南北朝时期就已应用于刀兵器。
宋代的文献资料较为丰富,使人们对夹钢刀剑的认识更为清晰。沈括在《梦溪笔谈》中提到古剑的特点:
古人以剂钢为刃,柔铁为茎干,不尔则多断折。剑之钢者,刃多毁缺,巨阙是也,故不可纯用剂钢。[15]
“剂”,齐也,从刀从齐,齐亦声,在指切。[16]“剂”,剪齐也,南方人呼剪刀为剂刀。[17]“剂”相对于“柔”,意为坚硬,柔铁指可锻铸铁或熟铁。剂钢作为刃口,较柔铁具有更强的斩切力,究其原因,田长浒认为,剂钢是指经过渗碳和淬火的碳钢[18],这种解释取“剂”的调节之意。“巨阙”取自《越绝书》:“欧冶乃因天之精神,悉其伎巧,造为大刑三、小刑二,一曰湛卢,二曰纯钧,三曰胜邪,四曰鱼肠,五曰巨阙。”[19]“巨阙”为古代名剑,钝而厚重,相传为春秋时期铸剑名师欧冶子所铸,“阙”通“缺”,意为残缺,因锋刃处有一缺口而得名。文中并未提及夹钢一词,但相比《考工记》郑注、贾疏隐晦的描述,指明了刀剑不同部位应具备的材质特性。工匠也认识到用全钢做的刀剑,刃部大多会损毁且容易断裂,“巨阙”就是这样的剑,而以钢为刀刃和以铁为刀身,实现“钢”和“铁”的复合则能避免折断。
以上文献较隐含地说明了夹钢工艺及夹钢刀剑具有刚柔相济的优点,而“夹钢”一词最早出现在文艺作品中,在董解元《西厢记》中用于描述兵器:
那法聪唤做真实取胜,怎知是飞虎佯败。把夹钢斧擗在战鞍,伸靴入镫,扳番龙筋弩,安上一点油,摇番铜牙利,会百步风里穿杨,教七尺来僧人怎躲?[20]
“夹钢斧”已明确表明兵器手斧[21]采用了夹钢复合技术,即钢被锻焊于斧体中间作为刃部。宋朝的强敌来自北方少数民族骑兵,以步军为主、骑兵为辅的宋军在骑战中显然处于劣势,取胜主要靠步战。宋兵所持斧钺用来砍斫敌人的攻城器具,斩截敌舰帆缆等,而夹钢的特性恰能满足这种使用要求,不仅应用在刀剑兵器上,而且也用在斧兵器上。[22]
将我这夹钢斧绰清泉,触白石上嗤嗤的新磨净。[23]
文中“绰”同“焯”,意为淬火。采用“清泉”作为淬火剂和“白石”作为磨石,表明古代匠人已掌握提高夹钢斧性能的方法,也反映出他们对淬火介质和磨石的选择已有丰富的经验。
明代《武备志》记载的“夹钢”是从兵器耗材的角度描述:
夹钢能用于制备大批量箭簇耗材,反映了明代锻焊复合技术的高度成熟。箭簇的复合工艺在战国至两汉应用较广。战国时代,以铁为铤,以铜为簇。东汉以后,可锻铸的铁簇就代替了铜簇。([18],261页)相比而言,夹钢箭簇会更坚硬且具有更强的穿透性。射出去的箭簇,很难回收再磨砺,故采用夹钢能节省更多钢材。由此可见,冶铁和夹钢技术促进了箭簇材质的转变。
明代宋应星的《天工开物》全面总结了钢铁刀剑复合工艺的特点:
凡铁兵,薄者为刀剑,背厚而面薄者为斧斤。刀剑绝美者以百炼钢包裹其外,其中仍用无钢铁为骨。若非钢表铁里,则劲力所施,即成折断。其次寻常刀斧,止嵌钢于其面。即重价宝刀,可斩钉截凡铁者,经数千遭磨砺,则钢尽而铁现也。倭国刀背阔不及二分许,架于手指之上不复欹倒,不知用何锤法,中国未得其传。凡健刀斧,皆嵌钢、包钢,整齐而后入水淬之,其快利则又在砺石成功也。[25]
性能卓越的刀剑以“百炼钢”包裹在外,熟铁作茎干和骨架,使用时能避免折断。为了便于与外铁内钢的夹钢工艺区分,这种外钢内铁的工艺称为包钢。由包钢制备的刀剑虽刃口锐利坚硬,但打磨次数过多后,里面的铁芯露出,便丧失了斩切力。通常所用的刀和斧,将钢嵌入其中,称为“嵌钢”,其实也是夹钢的另一种形式。《天工开物》记载:“凡凿,熟铁锻成,嵌钢于口。”([25],47页)文中虽未提及“夹钢”二字,但包钢和嵌钢类似于夹钢,都以钢作刃口,后续都经过淬火及磨砺。随着百炼钢和淬火技术的发展和成熟,最晚到明代,我国已形成完备的钢铁复合技术体系,夹钢工艺也衍生出包钢、嵌钢等其他复合工艺。显然,明代工匠的复合工艺技术最为成熟,并且对不同性能要求的兵器及工具采用何种复合工艺的认识已非常深刻。
纵观文献记载,汉代成熟的炼钢技术促进了“好钢用在刀刃上”复合技术的发展,为夹钢工艺奠定了技术基础。南北朝时期灌钢的发明,使夹钢刀剑中的“钢”来源多样化。元代之前的文献虽未出现“夹钢”词语,但却表明性能优越的刀剑多以钢为刃、铁为茎两种材质的复合。“夹钢”第一次出现在元曲中,用以形容兵器。夹钢由“幕后”到“台前”的过程恰反映了夹钢工艺逐渐走向成熟以及古代工匠对夹钢的理解不断加深。明代文献涉及的“夹钢”揭示了部分工艺细节,工艺的成熟表现在夹钢用于制备大批量箭簇耗材,所以,明代是夹钢技术的集大成期。夹钢的起源和发展并不能简单归结为“夹钢”二字的出现,而是源于古人对钢和铁两种性能及技术的深刻理解。
从金属加工角度来讲,夹钢工艺的本质是将钢和铁焊接在一起。“銲”是“焊”的早期字形用“金”字旁,强调熔合、连接金属。古代焊接主要分为铸焊(亦称浇焊)、钎焊和锻焊(锻接)[26],锻焊则多用于钢和铁的结合,为夹钢的基本方法,而锻焊却离不开焊药的使用。
郑复光在《镜镜冷痴》中记载:“铜铁焊用焊药参硼砂。”[27]《本草纲目》记载:“硼砂,能柔五金,而去垢腻。”[28]“去垢腻”就是去除焊药所造之渣。刘岳云所撰的《格物中法》提到:“卤盐制四黄,作焊药。同硇砂罨铁,一时即软。”[29]卤盐(MgCl2·6H2O)、硇砂(紫硇砂为NaCl,白硇砂为NH4Cl)和硼砂(Na2B4O7·10H2O)加热呈酸性,与金属氧化物发生氧化还原反应,形成的熔渣能隔离外界空气,因此,在焊铁时,起到造渣的作用[30],以达到“去垢腻”。以上文献记载中的焊药虽未指明用于何种焊接方式,但却表明了焊药的作用,而关于锻焊钢铁所用的焊药记载见于《天工开物》:
凡铁性逐节黏合,涂上黄泥于接口之上,入火挥槌,泥滓成枵而去,取其神气为媒合……凡焊铁之法,西洋诸国别有奇药。中华小焊用白铜末,大焊则竭力挥锤而强合之。历岁之久,终不可坚。故大炮西番有锻成者,中国则惟恃冶铸也。([25],44-45页)
凡舟行遇风难泊,则全身系命于锚。战船、海船有重千钧者。锤法先成四爪,以次逐节接身。其三百斤以内者,用径尺阔砧安顿炉傍,当其两端皆红,掀去炉炭,铁包木棍夹持上砧。若千斤内外者,则架木为棚,多人立其上共持铁链,两接锚身,其末皆带巨铁圈链套,提起捩转,咸力锤合。合药不用黄泥,先取陈久壁土筛细,一人频撒接口之中,浑合方无微罅。盖炉锤之中,此物其最巨者。([25],47-48页)
文中反映了“接铁”的两个关键步骤:一是在接口结合处涂上黄泥。黄泥的化学成分以SiO2、Fe2O3和Al2O3为主,取材广泛,制备简单,体现了古人善于运用自然造物的智慧。直到20世纪60年代,我国的夹钢采伐斧仍是用黄泥作为锻接剂[31];二是通过加热锤打,去除泥渣。文中提到的“神气”便是加入黄泥后与锻接面发生化学反应所产生的热量,体现了古人朴素的唯物主义观。对于焊铁的方法,西洋有“奇药”,而中国的“大焊”(锻焊或硬钎焊[32])没有用“药”,仅靠锤锻强行接合所制备的铁器并不耐用,所以,西方工匠能锻成大炮源于他们在锻接中善于使用焊药,而中国工匠则更擅长通过铸造来制备大炮。
锻接所用的焊药除了黄泥,还有“陈久壁土”。图2展示了古代工匠对“千钧锚”的锤锻,所用是筛细的旧墙土,日久返硝[33],墙硝主要为盐碱,遇热分解出氧气,从而提高焊接温度。锻焊铁时,烧红的接口与空气接触,表面会生成氧化铁皮,进而影响接口处的结合,冷却后容易形成缝隙,而撒入的旧墙土细末与氧化铁形成低熔点的液态硅酸盐[34],经锤锻被挤出结合处,达到“浑合”“无微罅”的效果。
图2 《天工开物》锤锚图
综上所述,中国古代接铁所用焊药为黄泥或旧墙土细末,取自生活场所或自然界,类似的焊药是否依然应用于当代夹钢工艺,以及焊药的化学原理仍需进一步探讨。
文献史料描述的夹钢是否存在,其金相组织有何特点,考古发现的铁器制品为此提供了重要的实物证据。表1为出土的夹钢制品分析。
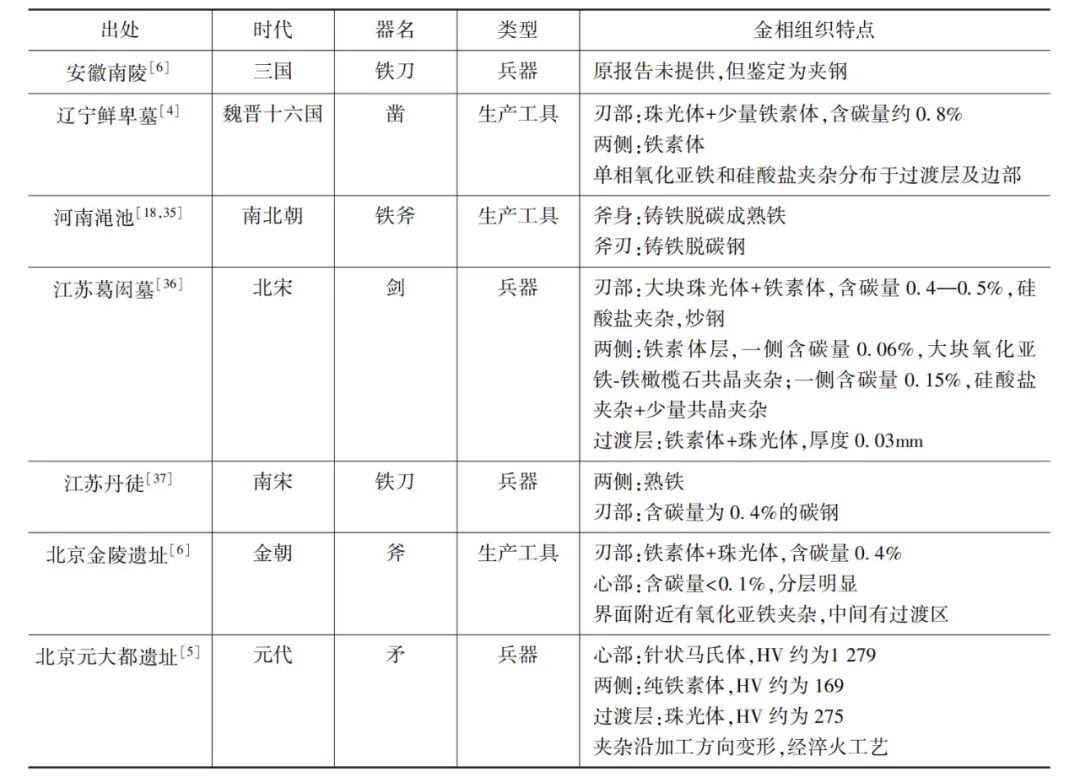
如表1所示,出土的夹钢制品主要用于生产工具和兵器,分布于辽宁、河南、北京、安徽和江苏,时代跨度从三国至金元时期。根据出土三国时期的铁刀,结合夹钢古文献的记载,可以推断夹钢起源于汉魏时期。夹钢刃口采用的炒钢和铸铁脱碳钢不仅佐证了古文献中“汉时斧近刃,皆以刚铁为之”的说法,而且反映了自汉以来铁器刃口材质来源广泛的事实。这是因为战国晚期炒钢技术的应用[38],极大地提高了炼钢的效率,与先前的铸铁脱碳技术共同完善了铁器生产制作体系。至东汉时期,生产工具和兵器已完全铁器化,为夹钢工艺奠定了原料基础。两宋时期,由于铁产量激增,煤炭被广泛应用,冶炼技术有了新发展[39],炒钢、灌钢技术的进一步推广使得夹钢制品的质量更好,成熟的百炼钢技术促进了锻焊夹钢技术在刀剑兵器上的应用。元代,夹钢应用范围进一步扩大至矛兵器。
纵观各个时期夹钢制品的组织特点,其刃体组织以珠光体和铁素体为主,两侧组织为铁素体,典型器物凿的金相如图3所示。元代,夹钢刃部为马氏体,如图4所示,经过淬火提高了硬度,为1279HV,印证了元代杂剧中“夹钢斧绰清泉”所体现的淬火过程。从各个时期夹钢刃部的含碳量进行分析,除了魏晋时期的凿含碳量较高外,其他时期的夹钢制品含碳量均为0.4%。由此可以看出,古代工匠们逐渐认识到夹钢刃部与两侧的材质具有一定差别时,才能更好地发挥夹钢的性能,并且刃部为中碳钢最适合。在鉴定夹钢时,因为夹钢制品是两种含碳量不同的材料,其界面较为明显,过渡层较薄,所以通过对其心部(刃口)含碳量高和两侧含碳量低的组织特点进行鉴定。除此之外,过渡层的厚度和夹杂物可以辅助鉴定。一般情况,夹杂物多为氧化亚铁和硅酸盐,沿着加工方向变形,分布于过渡层附近,所含元素成分在心部和两侧会有差异。
图3 凿的中心部位组织[4](x100)
图4 铁矛刃钢针状马氏体组织[5](x250)
夹钢工艺的难点在于不同成分的钢材锻焊成一体,容易产生裂纹、夹杂等缺陷,影响界面的结合,并且史料中没有记载完整的工艺细节。为了弥补史料之阙,笔者对阿昌族户撒刀的传统工艺,展开田野调查。
户撒乡位于云南省德宏州陇川县境内的高黎贡山与缅甸接壤的地方,是全国最大的阿昌族聚居地。阿昌族善于农耕和锻造,著名的户撒刀就是阿昌族工匠锻造技艺的代表。《新纂云南通志》记载:“户撒、腊撒两长官司地所制之长刀,铁质最为精炼,与木邦刀无二。”[40]明清至今享有盛誉,其原因为明军驻守屯垦于户撒,阿昌族人吸收了汉族的兵器制造技术的优点,形成了独具特色的锻制技艺。阿昌族打铁以家庭作坊式为主,打制刀具的原材料为回收的废旧铁料或钢板。他们打制的刀具产品除了在本地销售外,也远销西藏、青海等地方。随着互联网经济及当地旅游业的发展,许多外地客商和国内外的收藏家也慕名而来,产品价格从百元到上万元不等。阿昌族传统打铁的设备为木制风箱、铁、锤、钳、砧、泥石混合而成的火炉等。现代打铁与过去相比,其主要变化是空气锤代替手工锻打,砂轮机代替手工磨削,电驱动风箱代替人工手拉木质风箱,现代机械设备制刀取代传统手工锻刀的趋势较为明显。
笔者调研了老铁匠余绍美和其子余宽茂锻打户撒夹钢刀的工艺过程,主要工序如下所示。
(1)备料加热:从回收的废旧钢铁中挑选出熟铁和钢料,截取尺寸约140×40×20 mm熟铁料作为刀本体,成分接近低碳钢(20钢),截取另一小段尺寸约140×20×10 mm钢材作为刀刃,成分接近中碳钢。为了减少变形抗力,将其放置火炉中加热,燃料为木炭。从理论上讲,根据铁碳合金相图确定锻造温度[41],低碳钢的始锻温度约为1250℃,随着含碳量的增加,始锻温度将下降,因此中碳钢的始锻温度为1200℃,温度过高将导致过烧。为了避免过烧情况的出现,在保证所夹钢料未烧坏的情况下,适当降低本体钢(低碳钢)材料所允许的最高始锻温度,确定为1150—1200℃,两种材质的终锻温度为800℃。在实际操作中,工匠将根据锻件的火色来确定锻打时机,当锻件颜色接近亮黄色时开始锻打,亮黄的火色温度为1100—1200℃,接近理论上的始锻温度。
(2)夹钢:将铁料取出并放在砧子上,两个人相互配合,其中师傅一只手拿着钳子稳住铁料,另一只手拿着小锤不断敲打,徒弟抡大锤按照师傅敲打的位置进行锻打,如图5a所示。通过锻打使熟铁坯料和中碳钢变形拉长为长条形和短条形,然后将长条熟铁弯曲,并将短条中碳钢放在长条熟铁中,放置过程需要满足短条中碳钢有少许露头,锻打成心部为中碳钢、两侧为熟铁的三层结构,如图5b和5c所示。为了使两种材料更好地黏合,在两者的结合面上加入类似黄泥的砂土作为“焊药”,通过加热烧红后取出,并锻打为一体,如图5d和5e所示。在锻打过程中,当锻件的颜色变为赤红色或暗红色时,停止锻打,且继续放入炉中烧红,重复锻打直至打制成刀形,如图5f所示。
图5 户撒刀夹钢工艺过程
(3)淬火:也称“蘸火”。将刀加热至赤红色时,投入水中,当没有“呲呲”响声和白气时,取出留有余温的刀,冷却至室温。从理论上讲,中碳钢的淬火温度为810—830℃[42],在实际的操作中,刀匠凭借经验观察,当刀的火色变为赤红色时进行淬火,此时的温度接近理论温度。淬火介质包括水、青苔水、盐水、掺土的水和油,刀匠根据使用性能选择淬火介质。淬火决定了户撒刀的质量,目的是提高刃口的硬度,但淬火经验作为秘方并不外传。
(4)磨刃:在砺石上磨刀的两面,并露出中碳钢作为刃口,如图5g所示。刀的锋利不仅取决于硬度,也取决于开刃的角度,刀刃磨得越薄,所形成的夹角越小,就越锋利。
(5)试锋利度:吹毛断发,即把头发放在刀上,如果吹一口气能斩断,则证明刀非常锋利。借鉴此法,可以切刮腿上汗毛以试锋利,如图5h所示。
户撒刀的传统工艺,不仅印证了古文献中夹钢的淬火及磨刃,而且反映了铁匠们丰富的锻刀经验,如刀匠对火色的准确把握、撒入的“焊药”等,但这些经验背后所蕴含的科学理论需要进一步探讨。
通过检测分析户撒刀夹钢样品的微观组织及显微硬度,揭示传统工艺背后所蕴含的金属学理论,为探究界面结合及焊药等问题提供了科学依据。在样品分析过程中,利用线切割在户撒刀的刃部截取10×5×2 mm样品,经过热镶、磨光和抛光,使用浓度为4%硝酸酒精进行侵蚀,并在UM203i金相显微镜下观察界面组织;利用剑桥S250MK3扫描电子显微镜,配N10000能谱仪对样品的成分及夹杂物测定;利用载荷力为100g的HV-1000型维氏硬度计,在不同显微组织上均匀打点,得出显微硬度,并取其平均值,绘制成曲线。从宏观上看,刀具表面平整光洁,夹钢处无裂纹,如图6a所示;经过侵蚀后有明显的夹钢线,如图6b所示。
图6 样品制备(a 户撒夹钢刀;b 样品)
刀体两侧组织以铁素体为主,含有少量珠光体,晶粒大小均匀,如图7a所示。因为碳化物析出相易于被腐蚀,所以心部夹钢层的金相组织呈现稻草色,说明经历了低温回火。虽然整个过程中并未刻意回火,但由于“蘸水”冷却时间较短,利用自身的余温进行了自回火过程,使组织应力减小,变形倾向小[43],从而避免了由淬火脆性所导致界面结合不牢固的问题。
图7 样品金相组织
刀体两侧组织与心部夹钢层存在深灰色过渡层,由心部夹钢层中的碳扩散所致。过渡层组织以珠光体和低碳马氏体为主,两侧组织经过渡层与心部组织达到冶金结合,界面结合良好,没有发现裂纹、孔洞缺陷,如图7b所示。夹杂物沿加工方向呈点链状分布,如图7c所示。在刃口的尖端,随着横截面的减小,两侧材料所占比例逐渐减少,越接近尖端,两侧组织中铁素体含量越少,而珠光体含量越多,如图7d和7e所示。刃口尖端,冷却速度最快,为针状高碳马氏体组织,如图7f所示。
为了进一步分析元素扩散情况,对界面进行线扫描,元素分布特征如图8所示,两侧组织的Fe和C曲线变化较为平缓,但在心部发生突变,即Fe的曲线处于波谷时,C的曲线处于波峰,说明心部含碳量较高。C元素含量从两侧向心部逐渐升高,是界面达到冶金结合的重要依据。界面C曲线波谷到波峰的水平距离很短,说明两侧和心部之间过渡层较薄,保证了两种材质各自的特性。
图8 界面线扫描
从夹杂物的能谱分析可知,单相夹杂物较少,多为复相夹杂。处于不同部位的夹杂物的Si含量波动明显,单相夹杂物中Si含量要比复相夹杂物中Si含量高。靠近刀边缘部位的夹杂物,分为线状1和团絮状2。团絮状夹杂以球状氧化亚铁为主,线状夹杂除含有铁的氧化物外,含有较高的Si和Mn,系2FeO·SiO2及MnO·SiO2硅酸盐所致,Al和Ca的成分含量1.3-1.7%,系添加的砂土“焊药”致使夹杂中含有该成分,如图9和表2所示。界面附近的复相夹杂物以氧化亚铁为主,Si含量较边缘处含量低,为0.86%,没有Al和Ca元素,如图10和表3所示。结合金相图7b,界面附近铁的氧化物为脆性夹杂物,随着压力增加而破碎,沿金属变形方向呈链状分布,在明视场下呈灰色或暗灰色。
图9 刀边缘夹杂物形貌

图10 界面附近夹杂形貌

在锻焊中,空气中的氧不仅与金属铁表面发生氧化作用生成氧化皮(主要成分为Fe3O4[44]),还与二氧化碳、水蒸汽等发生反应生成铁氧化物。在此过程中,铁离子由内层向外表面扩散,氧化性气体则以原子态由外表面向内扩散。由于外表面氧化性气体较多,易形成Fe2O3,内层则形成FeO,由外向内氧化程度逐渐减轻。这些熔点较高的氧化铁不仅使夹钢层和两侧铁料的黏合变得困难,而且锻后在界面易形成夹杂物。过多的夹杂物使刀在承受较大冲击时易发生断裂,而在高温锻焊时,在两个接触面加入砂土焊药则能有效避免以上问题。砂土的成分以二氧化硅(SiO2,石英)为主,也有少量Al2O3及CaSiO3,高温下的二氧化硅和氧化铁的反应为2FeO+SiO2→2FeO·SiO2,其产物熔点较低,约为1177℃[45],呈液态分布在两块坯铁的表面。这种液态的铁渣不仅具有粘合剂的作用,而且可以隔绝空气,防止铁继续氧化,有益于界面的冶金结合。通过敲打附着在锻接的表面上熔渣层,便能轻易去掉,而内部液态的夹杂物经过锻打挤出。对比两侧边缘及界面夹杂,两侧边缘处Al和Ca及硅酸盐证明了焊药与氧化铁的反应,但在界面附近,只有氧化铁夹杂,并无焊药成分,说明锻焊时对界面结合处锻打充分,焊药和氧化铁反应彻底,并将反应产物挤出界面。结合金相,界面结合良好,焊药起到了黏合作用,但从中也可以看出,无论是界面还是两侧都含有铁的氧化物,说明彻底消除接触面上的氧化物是很困难的。
以刀的端面为起点,分别沿两侧和心部的a、b、c三个方向每隔2 mm的位置进行3次显微硬度测量,如图11所示,并取其平均值绘制曲线,结果如图12所示。两侧本体钢的硬度明显低于心部刃体,心部平均硬度为800HV,两侧平均硬度为350HV,结合金相组织及线扫描可知,淬火后形成的马氏体使得心部组织的硬度明显提高。两侧含碳量较低,导致低碳钢材料淬硬性差,淬火后硬度虽略有提升,并未发生明显变化。本体钢的材质为较软的低碳钢,淬火时变形小的性能特点能夹固住其中的刃钢,减小刃钢在淬火时的变形和开裂。界面附近硬度测试曲线如图13所示,过渡层硬度比两侧硬度高而比心部硬度低,说明硬度过渡平缓,减小应力开裂倾向。因此,高硬度组织确保了刃口的强度和耐磨性,硬度较低的两侧组织确保了刀的韧性,通过过渡层实现两种金属的力学性能互补,达到刚柔相济的效果。
图11 显微硬度测试点
图12 显微硬度曲线
图13 界面附近显微硬度曲线
本文基于文献史料和考古实物对夹钢工艺进行了梳理,研究表明夹钢起源于汉魏时期。随着古人对夹钢性能的认知越来越深入,夹钢制品的应用范围拓展至生产工具和兵器领域。伴随着中国古代钢铁技术体系的成熟,夹钢中的刃体主要包括炒钢和铸铁脱碳钢。从现有的文献和考古材料分析中,可以得知主要历史阶段夹钢的金相组织特点,但夹钢工艺的发展历程无法得以全面呈现。
通过对阿昌族户撒刀的工艺调查和样品的材料分析,得知影响夹钢界面结合的主要因素为焊药和自回火。淬火后户撒刀的两侧组织为铁素体和珠光体,心部组织为回火马氏体,刃口尖端为高碳马氏体,过渡层组织为珠光体和低碳马氏体。通过线扫描显示发现C元素含量从两侧向心部逐渐升高,进一步表明夹钢界面达到了冶金结合,源于自回火过程能减小淬火后界面的开裂倾向。显微硬度测试结果反映了组织的强韧性,心部平均硬度800HV,两侧平均硬度为350HV,体现了夹钢刀的刚柔相济性能。过渡层硬度高于两侧低于心部,避免了过渡层硬度的突变和开裂。夹杂物的能谱分析表明,在高温下,含有SiO2的砂土焊药与锻接表面的氧化铁,形成低熔点的液态硅酸盐,而焊药的作用为造渣,此过程进一步揭示了古文献记载“黄泥”和“陈久壁土”的化学原理。
致谢:感谢主编和审稿专家提出的宝贵意见。在调查过程中,得到了老铁匠余绍美和其子余宽茂、国家级非遗传承人项老赛和其子项红安、陇川县文化和旅游局非遗中心主任闫瑾,以及博士生卜超群和陈苹的帮助。在此一并致谢!